Apprenticeships prepare Red Lake members for jobs
Go Deeper.
Create an account or log in to save stories.
Like this?
Thanks for liking this story! We have added it to a list of your favorite stories.
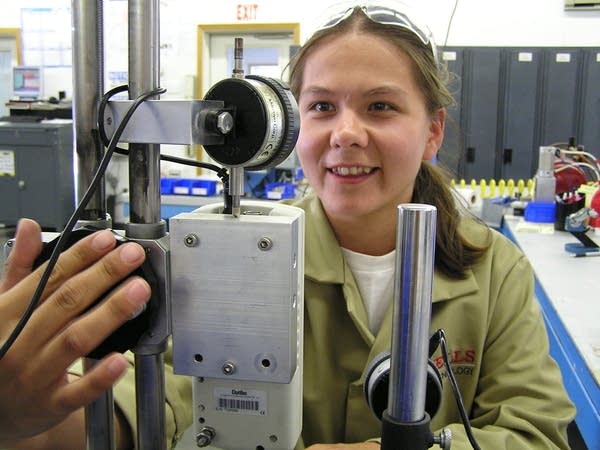
Manufacturing industries employ about 20 percent of the workforce in the U.S. but proportionately, few of those workers are Native American. That doesn't make sense to Andy Wells. He gets frustrated when he thinks about the number of people in tribal communities who are out of work.
"Back in the 1930s and the Great Depression, they talk about 30 percent unemployment in America and it was a crisis," said Wells. "We have double that on the reservations; 60 percent. We need to do something, especially those of us who are members of the tribe, to help our own people."
[image]
Wells learned the value of work growing up on a farm on the Red Lake reservation. As a young man, he discovered he had a knack for industrial design. Working for Polaris Industries in Roseau, Wells designed one of the first front-engine snowmobiles.
Turn Up Your Support
MPR News helps you turn down the noise and build shared understanding. Turn up your support for this public resource and keep trusted journalism accessible to all.
After teaching industrial technology for 20 years at Bemidji State University, Wells started consulting for large companies. In the late 80s, he invented an air-powered scissors to solve a carpal tunnel injury problem for line workers at the Gold'n Plump poultry plant near St. Cloud. The scissors are one of a half-dozen inventions Wells has patented.
Today, Wells Technology, Inc. manufactures some 10,000 different parts for various industries; things like metal fasteners for jet engines and military vehicles, electronic components for computers and parts for airplanes and medical equipment.
The company employs 31 people, double what it was just three years ago. The rapid growth has meant a shortage of skilled machinists to run the facility's high-tech equipment. That's when Wells decided to create Wells Academy. Using some grants and his own money, Wells provides seven paid apprenticeships to members of the Red Lake Band of Ojibwe.
I think if we want to strengthen America, we have to strengthen these pockets of poverty that exist... We talk about the land of opportunity, but it isn't opportunity for everybody.
The program is designed to take about a year to complete, but Wells is flexible and allows participants to progress at their own pace. It will eventually provide his company a stream of skilled workers. But Wells says he's more interested in providing new learning opportunities for young Red Lake tribal members. Graduates are under no obligation to stick with the company, Wells says he's happy just to get a few more Native Americans interested in manufacturing careers.
"I think if we want to strengthen America, we have to strengthen these pockets of poverty that exist," said Wells. "Instead of giving CEOs another $10 million, we need to do something for the people who are really struggling in this America. We talk about the land of opportunity, but it isn't opportunity for everybody. Some have to have training first."
Next month, Wells Academy will produce its first graduate. Dave Bedeau, 19, says he plans to further his education at Bemidji State University, then maybe join the Navy.
"I see myself as getting a foot in the door, you know, getting training," said Bedeau. "When I got out of high school I was interested in machining. I found out they had the academy started up, so I was just right place, right time, I guess."
All of the Wells Academy apprentices are Red Lake Band members; about half are high school drop outs, some have been in trouble with the law. Jeff Hildebrandt, an instructor at the academy, says some have faced extreme poverty.
"We've had some of our students say that it's changed their life, and have actually said how this has really turned around their direction in where they were going," Hildebrandt said. "Some of our students go from a downward slide to really starting on an upward incline."
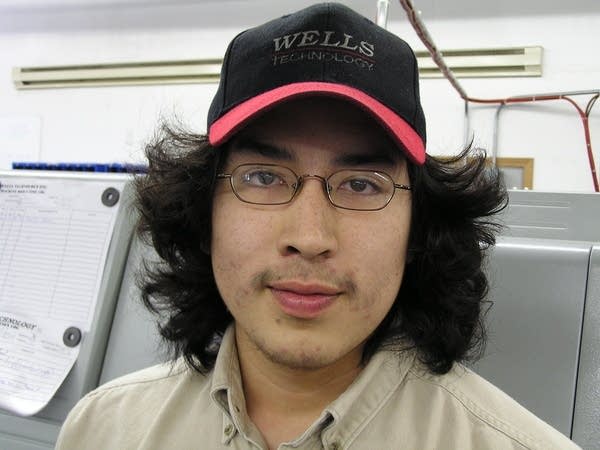
Some apprentices are committed to sticking with Wells Technology after they finish the academy. Randi Burris, 23, struggled in high school but graduated from an alternative learning center. Burris says the job outlook on reservations is bleak. She says Wells Academy is giving young Native Americans another option.
"It's really, really bad," said Burris. "It's really, really hard to find a good job, you know, that you'll have a steady, reliable workplace. You know, this place, it's opening up a lot of doors for us. It's quite nice."
Burris says the pay opportunities are nice, too. Apprentices start out at about $9 an hour, well above minimum wage. By the end of the program, they can earn close to $16 an hour. Andy Wells hopes to almost double the number of apprentices by the end of the year.